La Production
- ARTICLE 8
- 24 janv. 2016
- 3 min de lecture
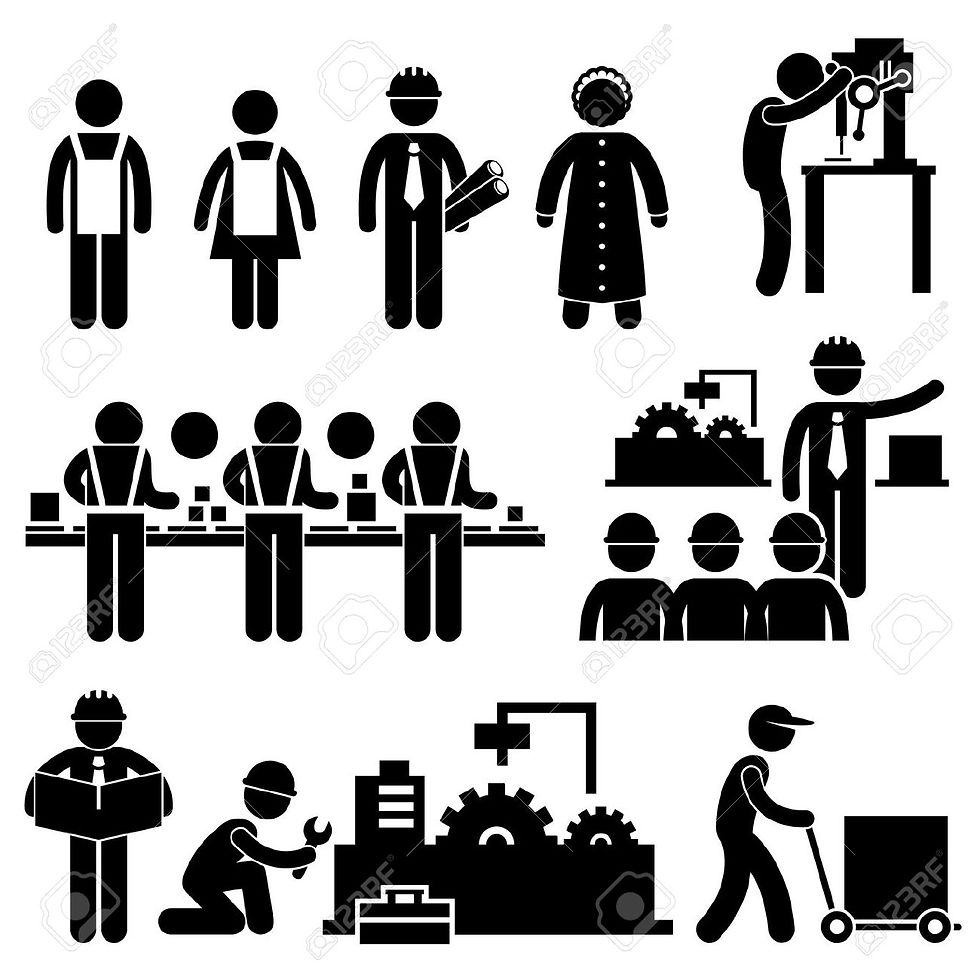
Le jean est porté et fabriqué partout dans le monde on estime qu’un jean fait 65 milles kilomètres durant son processus de fabrication (soit 1 fois et demi le tour de la Terre) des récoltes du coton en Asie puis de son assemblage en Tunisie et sa vente en Europe, aux USA, ou en Asie. Ses composants viennent des 4 continents avec du coton venant du Mali, de la Chine ou de l’Inde, une coloration « bleu indigo » allemande, du zinc pour les rivets d’Australie, du cuivre de Namibie pour les boutons, une fermeture éclair en provenance du Japon ou encore de la pierre ponce de Turquie pour le délavage : au total 18 composants sont utilisés de 12 pays différents (en moyenne).
Tout d’abord la matière de base du jean est le coton, on commence donc par le récolter à la main mais un homme ne peut ramasser que 50kg par jour une machine se charge maintenant de le ramasser, il ramasse 50kg en seulement 5min. Puis le coton est envoyé dans une usine, pour être nettoyé grâce à une machine triant les impuretés et le coton pur et le compacte en botte de 200kg (assez pour produire 325 paires de jeans).
Le coton est encore à son état naturel pour pouvoir obtenir un tissu il faut le fileter : il est d’abord étiré pour obtenir de la fibre, puis ces fibres sont enroulé sur une bobine.
Le coton subit ensuite une teinture : plongé dans une coloration liquide bleu puis à sa sortie la couleur est fixée sur la matière grâce à de l’hydrogène, le coton à maintenant sa coloration bleu indigo.
Le coton est ensuite tissé, pour cela les fils de coton (chaîne) sont entrelacés à un angle de 90 degrés avec des fils de coton blanc ou bleu (trame). Le tissage réalisé est très serré, le tissu obtenu prend alors son appellation « denim » contraction de « de Nîmes » (allusion au tissu « serge de Nîmes ») qui a alors la capacité d’être très résistant. Il est enroulé à son tour sur un rouleau.
Le denim arrive dans une autre usine destinée à la fabrication du jean, c’est la finition : les rouleaux de denim sont déroulés les uns sur les autres (100 épaisseurs à la fois) sur une table puis ils sont découpés selon des patrons (cette opération d’empilement permet la découpe de plus de jean en même temps), un logiciel permet de connaitre où découper pour perdre le moins de tissu possible réduisant les pertes à seulement 7% de l’ensemble d’un rouleau. Les petites pièces comme les poches sont taillées avec un « clicker » (emporte-pièce) il découpe à l’aide d’un moule coupant. Il ne reste plus cas assembler les pièces les unes aux autres : un jean est composé jusqu’à 1.6m de denim, 6 rivets et 5 boutons ou une fermeture éclaire, le tout réalisé en 15min. On commence la couture (avec un fil 100% coton), les poches, la boutonnière, les dessins des poches sont brodés, ensuite les boutons sont mis en place par pressions. Toutes les coutures entre morceaux de tissu sont réalisées à l’envers pour obtenir un tissu à l’endroit sans coutures, on ajoute la fermeture éclair grâce à une « crampeuse », ainsi que la ceinture de tissu qui est cousue. Enfin le jean est presque prêt, d’abord remis à l’endroit par une « tourneuse », puis le jean selon l’apparence voulu (délaver, trouer, griffer) est préparé puis presser à la vapeur. Maintenant il ne reste plus qu’à le plier avec une machine, l’étiqueter et l’envoyer à l’autre bout du monde.
Comments